Category
TAGS
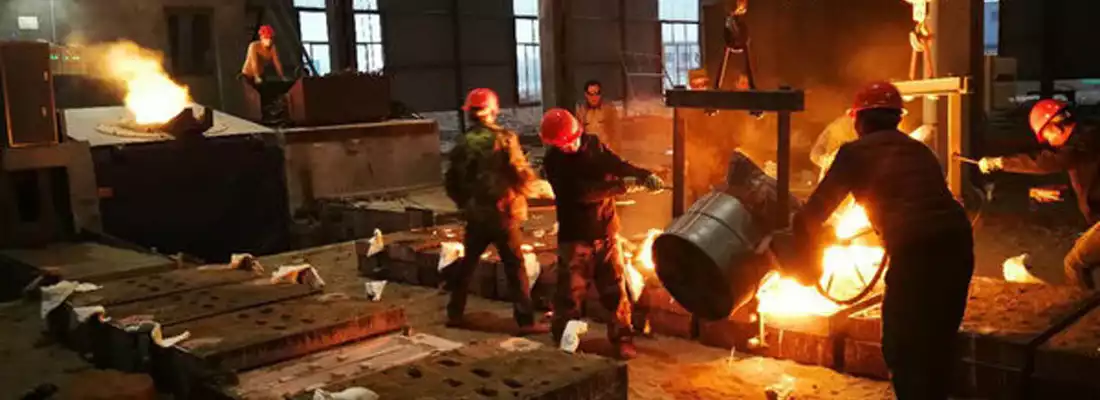
Induction Melting Furnace
The core role of intermediate frequency furnace in metal smelting
1. Efficient heating, energy saving and consumption reduction
Compared with traditional heating methods, intermediate frequency furnaces have the advantages of fast heating speed, high thermal efficiency, and low energy consumption. Since electromagnetic induction heating acts directly on the inside of the metal, reducing losses during heat transfer, the heating efficiency is significantly improved. At the same time, the intermediate frequency furnace can accurately adjust the heating power according to actual needs to avoid energy waste and achieve real energy saving and reduction.
2. Uniform heating to improve quality
When the intermediate frequency furnace is heated, the eddy current is evenly distributed inside the metal workpiece, so that the workpiece is heated evenly as a whole, effectively avoiding the local overheating or overcooling that may occur in traditional heating methods. This uniform heating method helps to improve the uniformity of the organization and mechanical properties of metal materials, thereby improving product quality.
3. Green and environmentally friendly, reducing pollution
The intermediate frequency furnace does not produce open flames and smoke during heating, and has high heating efficiency, reducing energy consumption and exhaust emissions, which meets the requirements of green development of modern industry. In addition, the medium frequency furnace is also easy to realize automatic control, reducing the pollution risk caused by manual operation.
4. Flexible and adaptable
Intermediate frequency furnaces can be widely used in the smelting and processing of various metal materials, including iron, steel, copper, aluminum, etc. Its heating power and frequency can be flexibly adjusted according to different materials and process requirements to meet the heating needs in different production scenarios.